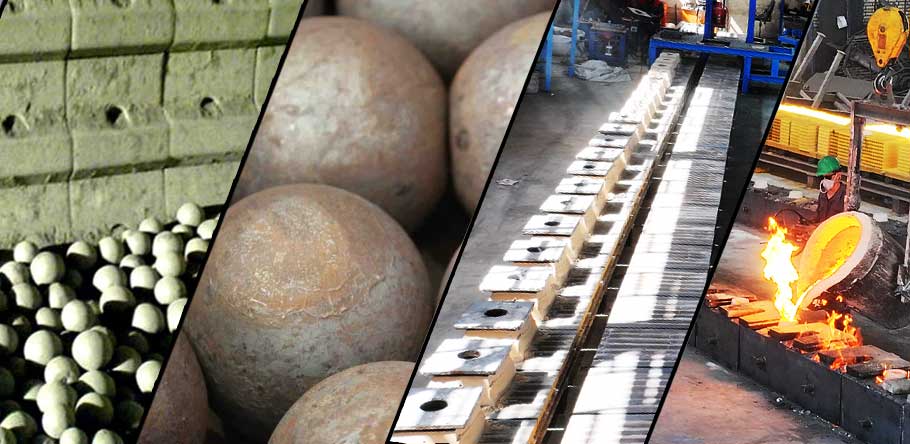
Cast iron grinding balls
Cast iron grinding balls are widely used components in various industries, playing a crucial role in the grinding process of mills.
The key features of these components include high wear resistance, resistance to breakage and deformation, and the ability to maintain a spherical shape during the grinding process.
A ball with suitable technical specifications is expected to possess these qualities. Another important indicator of this product is the wear rate of the balls, which determines their consumption speed during the process. Controlling this indicator significantly helps reduce production costs. A lower wear rate means reduced consumption and increased lifespan of the balls during the grinding and micronized powder production processes.
Grinding balls in ball mills for producing micronized powder have many applications and have special properties including the following:
- Chemical composition
- Mechanical hardness
- Dimensional and weight tolerance
- Other
The company manufactures these components in spherical shapes (in sizes 15, 17.5, 20, 25, 30, 35, 40, 50, 60, 70, 80, 90, 100, and 125 mm) and cylindrical shapes (in sizes 12×12, 16×16, 19×19, 22×22, 25×25, and 30×30 mm).
These components are primarily produced with the following standard analyses or customized analyses based on customer requests.
Chemical Composition and Hardness
Hardness HRC |
Max
%S |
Max
%P |
%Ni | %Cr | %Mn | %Si | %C | |
58-64 | 0.08 | 0.05 | 0.5 ≥ | 10-12 | 0.3-0.7 | 0.4-1.0 | 2.9-3.5 | No. 1 |
58-63 | 0.08 | 0.05 | 0.5 ≥ | 11-14 | 0.3-0.7 | 0.5-1.0 | 2.5-3.3 | No. 2 |
58-62 | 0.08 | 0.05 | 0.5 ≥ | 15-17 | 0.3-0.7 | 0.5-1.1 | 1.8-2.6 | No. 3 |
58-62 | 0.08 | 0.05 | 0.5 ≥ | 29-31 | 0.3-0.7 | 0.5-1.0 | 2.0-2.8 | No. 4 |
Min.48 | 0.1 | 0.05 | 0.5 ≥ | Max 2.5 | 0.3-0.9 | 0.5-1.0 | 3.0-3.9 | No. 5 |
* All these products can be consumed in different conditions in wet and dry Asia.
One of the most important characteristics of pellets is their size and dimensions, in addition, pellets are produced in different sizes in spherical and cylindrical shapes.
Dimension Tolerance of Grinding Balls
Units per MT | Weight
Tolerance(gr) |
Weight(kg) | Size(mm) |
71428 | ±2 | 0.014 | 15 |
45454 | ±2 | 0.022 | 17.5 |
29412 | ±4 | 0.034 | 20 |
15385 | ±5 | 0.065 | 25 |
8403 | ±10 | 0.119 | 30 |
3636 | ±15 | 0.275 | 40 |
1869 | ±25 | 0.535 | 50 |
1118 | ±40 | 0.894 | 60 |
678 | ±50 | 1.474 | 70 |
479 | ±50 | 2.087 | 80 |
338 | ±100 | 2.962 | 90 |
229 | ±100 | 4.360 | 100 |
123 | ±150 | 8.100 | 125 |
Dimension Tolerance of Grinding Balls
Dimension
Tolerance(mm) |
Diameter
(mm) |
Size (mm) |
-0.5 +1 | 15 | 15 |
-0.5 +1 | 17.5 | 17.5 |
-0.5 +1 | 20 | 20 |
-0.5 +1 | 25 | 25 |
-0.5 +1 | 30 | 30 |
-1 +1.5 | 40 | 40 |
-1 +1.5 | 50 | 50 |
-1 +1.5 | 60 | 60 |
-1 +2 | 70 | 70 |
-1 +2 | 80 | 80 |
-1 +2 | 90 | 90 |
-1 +2 | 100 | 100 |
-1 +2.5 | 125 | 125 |
Silpebs is the cylindrical shape of these balls, which usually have the same length and diameter.
Size, Weight, and Weight Tolerance of Grinding Sylpebs
Number/MT | Weight Tolerance(gr) |
Weight(kg) | Size |
88496 | ±1.5 | 0.0113 | 12*12 |
38197 | ±2 | 0.0262 | 16*16 |
22925 | ±4 | 0.0436 | 19*19 |
14917 | ±4 | 0.0670 | 22*22 |
10341 | ±5 | 0.0967 | 25*25 |
6053 | ±10 | 0.165 | 30*30 |
Dimension Tolerance of Grinding Sylpebs
Dimension
Tolerance(mm) |
Diameter
(mm) |
Size (mm) |
±1 | 12 | 12*12 |
±1 | 16 | 16*16 |
±1 | 19 | 19*19 |
±1.5 | 22 | 22*22 |
±1.5 | 25 | 25*25 |
±1.5 | 30 | 30*30 |
These pellets are mainly made of cast iron, which is an iron alloy containing a lot of carbon and some silicon and other elements. The special mechanical properties of cast iron, including hardness and high resistance to wear and impact, have made cast iron balls have a special place in industries such as mining, cement, power plants, and even chemical industries.
Composition and structure of cast iron pellets
Cast iron is an alloy that is divided into two main categories, white cast iron and gray cast iron, depending on the type and percentage of its compounds. This division is based on the formation of graphite in the microscopic structure of the alloy.
White Cast Iron
Due to its hardness and very high wear resistance, white cast iron is used more in the production of cast iron balls that must work in severe wear environments. In white cast iron, there is graphite in the form of iron carbide (Fe3C), which increases the hardness and brittleness of this type of cast iron. This type of cast iron is used in mining industries and heavy mills due to its high wear resistance.
Gray Cast Iron
In this type of cast iron, graphite is present in the form of fibers in its structure, which improves mechanical properties such as flexibility and shock absorption. Although the wear resistance of gray cast iron is lower than that of white cast iron, this type of cast iron is more suitable for conditions that require greater flexibility and impact resistance.
Features and benefits
- High wear resistance: The compounds in cast iron, especially in white cast iron, increase the surface hardness of these balls. This feature makes cast iron balls have an acceptable performance in the face of severe wear in grinding processes.
- Long useful life: Cast iron bullets have a longer lifespan than other types of bullets due to their high resistance to wear and corrosion. This helps to reduce maintenance and replacement costs.
- Reasonable production cost: Cast iron as a raw material is relatively cheaper than steel and some other alloys. Therefore, the production of cast iron balls can be economical for industries that need a large volume of these parts.
- High hardness and strength : cast iron balls, especially those made of white cast iron, have a very high hardness that It makes them suitable for heavy industrial applications.
Applications of cast iron pellets
Ball Mills: One of the most important applications of cast iron balls is in this type of mills, which are used in the process of crushing and pulverizing mineral and industrial materials. Ball mills convert hard materials into powder using these balls and are widely used in the mining and cement industries.
Mining industries: In mines, cast iron balls are used to crush stones and various minerals such as iron ore, copper, gold and other metals. These balls have a significant performance due to their high resistance to wear and corrosion in harsh mineral environments.
Cement factories: In the cement industry, cast iron balls are used to crush primary raw materials such as lime and clinker. The process of grinding raw materials using these pellets produces cement powder, which is a vital part of cement production.
Power plants: In power plants, cast iron pellets are used to grind coal into smaller particles that can be more efficient in the process of producing energy with fossil fuels. be
Chemical and pharmaceutical industries: In some chemical and pharmaceutical production processes, cast iron balls are used to crush materials. In these industries, the high resistance of these bullets is used to crush hard materials.
Challenges and limitations
Fragility of white cast iron: Although white cast iron has a very high hardness, due to its brittle and brittle structure, it may crack or break when exposed to strong blows. This issue can be problematic in some industrial situations.
Application limitations of gray cast iron: Gray cast iron has more flexibility, but its wear resistance is lower than white cast iron. Therefore, choosing the right type of cast iron for bullets depends on the type of operation and working conditions.
Cast iron balls are widely used in various industries due to their special characteristics such as high hardness, wear resistance and reasonable production costs. Choosing the type of cast iron (white or gray) based on working conditions and industrial needs is very important. Despite challenges such as the brittleness of white cast iron or the lower strength of gray cast iron, these balls are still considered one of the main choices in crushing and grinding processes due to their high efficiency and longevity.